SDMO Fabrication
Encourage Growth by Modernizing Your Fabrication Business.
Sage Distribution and Manufacturing Operations (SDMO) removes complexity and improves visibility in to not just inventory, but all aspects of your business. Having real-time data of your inventory levels and reorder points gives your business a competitive advantage.
When designing and maintaining item records, users are able to establish bills of materials (kits) and routings. Cost savings and margin gains will come naturally with component costing on the bill of material level. Routings plus labor reporting can help improve efficiencies on the production floor.
Fabrication orders are created to fulfill both make to order or make to stock items. Material and/or labor can be tracked on fabrication orders depending on what your business needs are. Users can enter completions on the fly for finished goods, keeping inventory updated in real-time.
Scheduling has never been easier than with SDMO’s calendar view with drag and drop capabilities. Seeing the overall workload by day, week, or month for a specific department allows production staff to easily see capacity levels. When a fabrication order needs to be rescheduled, it’s as simple as dragging and dropping it to the appropriate day. The calendar can be displayed on a digital dashboard for all production staff and to replace your current whiteboard.
All daily tasks will be modernized with simplified workflows and rapid data-entry screens in sales order entry and purchasing. As transactions are entered, reports are updated real-time allowing for operational visibility and swift decision-making abilities.
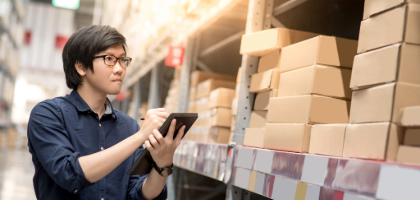
Improve Inventory Stocking
Reduce stock outs by using SDMO's Material Requirements Planning (MRP) functionality. Calculations can be done by site, item, or date and results are displayed immediately. Users can filter through purchasing and production requirements and react accordingly with the click of a button. With efficient inventory replenishments, orders are able to get out the door faster.
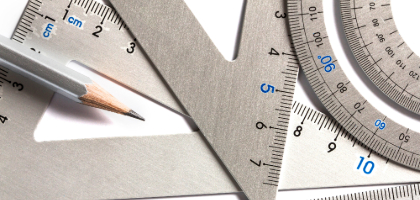
Flexible Units of Measure
SDMO allows you to define your industry specific units of measure (UOM) for how each item is stocked. In addition to the item's stocking UOM, a user can also define a selling and/or purchasing UOM with conversion factors. For example, an item can be purchased in pallets but stocked in eaches.
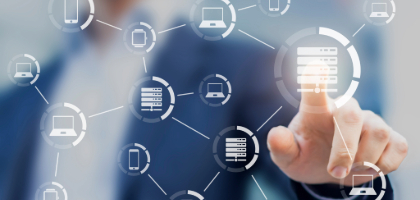
Industry Specific Routings
Routing steps are defined by you and your business during implementation. This promotes the flexibility of the software and ensures your user's experience feels natural. Routing operations can be as simple or as complex as your business needs. SDMO was developed with operational user in mind and ensures processes are simple and straightforward.
Built for Fabricators
- Data is displayed on user-friendly dashboards and reports that have drill-down capabilities
- Explore bill of materials within fabrication orders to see all associated orders
- Use note fields within vendor and customer transactions to collaborate internally
- Room to expand your business with multi-location, multi-currency, multi-lingual functionality